DIFFERENCES IN COLOUR AFTER NATURAL ANODIZING OF 6060 ALLOYS A THING OF THE PAST AT E-MAX
Differences in colour after natural anodizing are a thing of the past with the 6060 alloys from E-MAX. Following extensive studies carried out in collaboration with Vrije Universiteit Brussel, we have been able to identify important causes of difference in colour and, most importantly, how to prevent those differences. You can read more about it in this newsletter.
The causes of differences in colour
Differences in colour in aluminium profiles can occur whatever the aluminium alloy being used, whether traditional (or ‘primary’) or circular aluminium. With X-ECO (premium circular aluminium), however, we eliminate all differences in colour entirely. Post-doctoral researcher Alexander Lutz of Vrije Universiteit Brussel explains: ‘The main causes of differences in colour are the method used for anodizing and extrusion and the alloying elements that occur in the aluminium being used. It’s an unexpected and unparalleled complexity that has brought despair to many users for decades. ’
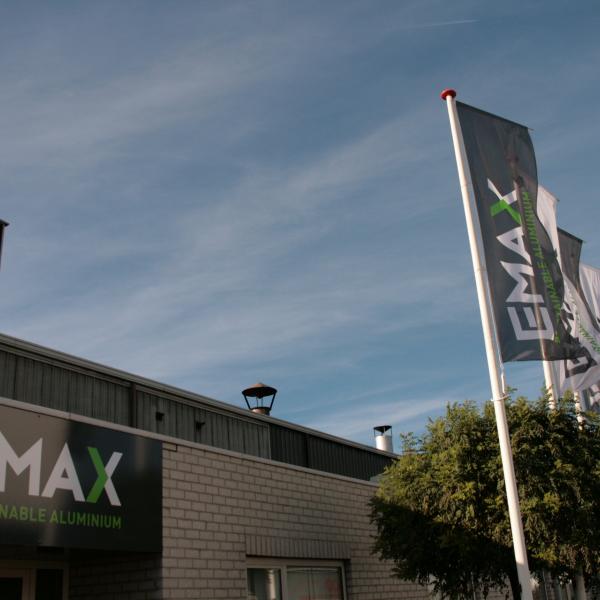
Main cause: the composition of the alloy
In addition to aluminium, E-MAX alloys contain a range of alloying elements, including silicon, magnesium, copper, zinc, manganese, and iron. Each one of these alloying elements has a major impact on the properties of the aluminium.
‘Iron has the greatest impact on how light the aluminium is,’ explains Lutz. ‘Alloys that contain more iron naturally have a darker appearance, which comes from the iron precipitates in the transparent natural anodizing layer. The thickness of the anodizing layer is an important determining factor. If you apply a thinner anodizing layer, there will be less iron in the layer, making the anodized aluminium more lightweight.’
The anodizing process as an influencer of colour
As mentioned above, the thickness of the anodizing layer plays a very important role, and the thicker the layer, the darker the profile. The thickness of the layer can be impacted by the following process parameters:
- Current strength: the higher the current, the thicker the anodizing layer and the darker the profile.
- Temperature: the higher the temperature of the anodizing bath, the thinner the layer and the lighter the colour.
- Time: the longer a profile is anodized, the thicker the layer. This in turn will make the profile darker as the length of anodizing increases. Importantly though, it is not just the duration of the anodizing process that is important, but the way in which the profiles are suspended in the baths.
Prevent differences in colour during anodizing
Sound expertise and good control over the process will help to prevent differences in colour, even when comparing profiles from multiple production batches. It is essential that you always choose professional and experienced anodizers who have demonstrated that they can fully manage the process.
Lutz explains: ‘As E-MAX keeps the alloy compositions of its circular aluminium within very narrow limits and fully manages the extrusion process, the company can offer a high-quality product. In addition, E-MAX also purchases traditional (or ‘primary’) aluminium within very narrow limits and can process it with X-ECO 6060.22 without any differences in colour.’
Other factors that affect appearance
There are, of course, other factors that affect the colour of aluminium, such as granule size, which can influence both the colour and shine of the profiles. Having the right composition in the pickling bath, and using the right additives, play another important role. Accordingly, it is important to work with professional chemicals suppliers, such as Metachem, Alufinish, A&D Chemicals, Henkel, etc.
Conclusion
Proper management of the extrusion and anodizing process can help to prevent differences in colour with X-ECO 6060 alloys and traditional alloys. Working with professional partners who manage every step of the production process helps to minimize the risk of differences in colour, which is why E-MAX has worked tirelessly over the past decade to build an extensive network of partners. In addition, we have also developed a method that allows us to process traditional and circular alloys together. Would you like further information? Please contact us. We would be happy to explain how it all works.